Expert Packaging Machine Repair Service to Keep Your Equipment Running Smoothly
Expert Packaging Machine Repair Service to Keep Your Equipment Running Smoothly
Blog Article
Recognizing the Secret Parts and Repair Strategies for Product Packaging Equipment Maintenance
Efficient maintenance of product packaging devices hinges on a thorough understanding of their crucial elements, including the frame, drive system, and securing devices. Acknowledging typical upkeep problems, coupled with the application of preventative methods and fixing strategies, can considerably improve maker integrity.
Secret Elements of Packaging Makers
Packaging makers include numerous essential parts that interact to make certain effective and efficient packaging processes. At the core of these machines is the frame, which gives structural integrity and houses the numerous operating parts. The drive system, usually a mix of gears and motors, facilitates the movement of parts, making it possible for specific procedure throughout the packaging cycle.
An additional necessary element is the conveyor system, which carries products via various stages of the packaging procedure. This is commonly matched by sensors and controls that monitor the placement and speed of items, ensuring synchronization and decreasing mistakes. The filling system is critical for properly dispensing the right amount of product into plans, whether in liquid, powder, or strong type.
Sealing devices, including heat sealants or sticky applicators, play an important duty in securing packages, avoiding contamination and extending rack life. Additionally, classifying systems are essential for supplying essential product details, making sure compliance with regulations. The control panel, furnished with straightforward user interfaces, permits operators to manage device features, monitor performance, and make modifications as needed, ensuring ideal performance and effectiveness in packaging procedures.
Typical Upkeep Problems
Efficient operation of product packaging equipments depends greatly on regular maintenance to avoid usual problems that can disrupt production. Among these problems, mechanical wear and tear prevails, especially in parts like seals, conveyors, and motors, which can result in unanticipated downtimes. Additionally, misalignment of components can result in inefficient procedure, creating items to be improperly packaged or damaged during the process.
One more common maintenance concern includes the buildup of dust and debris, which can disrupt the equipment's sensors and moving components. packaging machine repair service. This not just influences performance however can additionally present safety threats. Lubrication failings can lead to enhanced rubbing, resulting in overheating and ultimate part failure.
Electrical issues, typically originating from loose links or damaged circuitry, can disrupt machinery functions, bring about significant production hold-ups. Software application problems due to incorrect setups or obsolete programs can hinder the equipment's operation, necessitating immediate treatment. Attending to these usual upkeep issues proactively is vital for guaranteeing optimum efficiency and longevity of packaging machinery.
Preventative Upkeep Methods
Applying preventative upkeep methods is essential for maintaining the efficiency and dependability of packaging makers. These techniques incorporate an organized method to maintenance, concentrating on the regular evaluation and maintenance of tools to preempt possible failings. By sticking to a set up maintenance program, operators can recognize damage on components before they lead to substantial malfunctions.
Crucial element of a preventative upkeep approach consist of routine evaluations, element, lubrication, More Help and cleansing substitutes based upon supplier suggestions. Making use of lists can simplify this process, ensuring that no crucial tasks are overlooked. Furthermore, maintaining exact records of upkeep tasks help in tracking the maker's efficiency gradually, helping with informed decision-making pertaining to future upkeep demands.
Training personnel on the significance of preventative maintenance enhances conformity and fosters a society of proactive care. Applying an anticipating maintenance element, utilizing information analytics and sensing unit innovation, can further maximize equipment efficiency by predicting failings before they happen.
Repairing Methods
When confronted with malfunctions or inefficiencies in packaging devices, employing organized troubleshooting methods is crucial for determining and solving issues promptly. The initial step in reliable troubleshooting is to develop a clear understanding of the device's functional criteria and efficiency metrics. This includes assessing the equipment's specs, along with any kind of error codes or notifies displayed.
Next, operators need to perform a visual examination, looking for evident signs of damages, wear, or misalignment. This frequently includes analyzing sensing units, belts, and equipments to pinpoint potential root causes of malfunction. Collecting functional data, such as production rates and downtime logs, can likewise give insights right into recurring issues.
Once potential issues are recognized, utilizing a sensible technique to isolate the root reason is vital. This may call for screening private components or systems in a controlled way. Participating in discussions with drivers who interact with the equipment on a regular basis can yield beneficial comments about unusual behaviors or patterns.
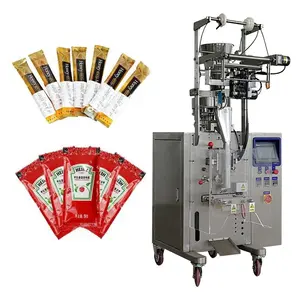
Repair Work and Substitute Ideal Practices
A detailed understanding of repair and replacement best techniques is important for preserving the long life and effectiveness of product packaging devices. Frequently assessing the problem of maker parts allows for timely treatment, protecting against more substantial problems that can lead to pricey downtimes.
When repairs are required, it is important to use OEM (Original Equipment Maker) parts to ensure compatibility and performance. This not only protects the integrity of the maker but also maintains service warranty arrangements. Furthermore, it is suggested to maintain an inventory of crucial extra components to facilitate quick replacements and decrease operational disturbances.
For complex fixings, involving certified specialists with specialized training in packaging machinery is recommended. They possess the competence to identify issues accurately and perform repairs successfully. Recording all repair tasks and components replacements is important for keeping a detailed maintenance background, which can aid in future troubleshooting.
Finally, executing a proactive method, including routine examinations and straight from the source predictive upkeep strategies, boosts the dependability of packaging devices. By adhering to these best methods, companies can make certain optimum maker performance, decrease operational risks, and prolong equipment life expectancy.
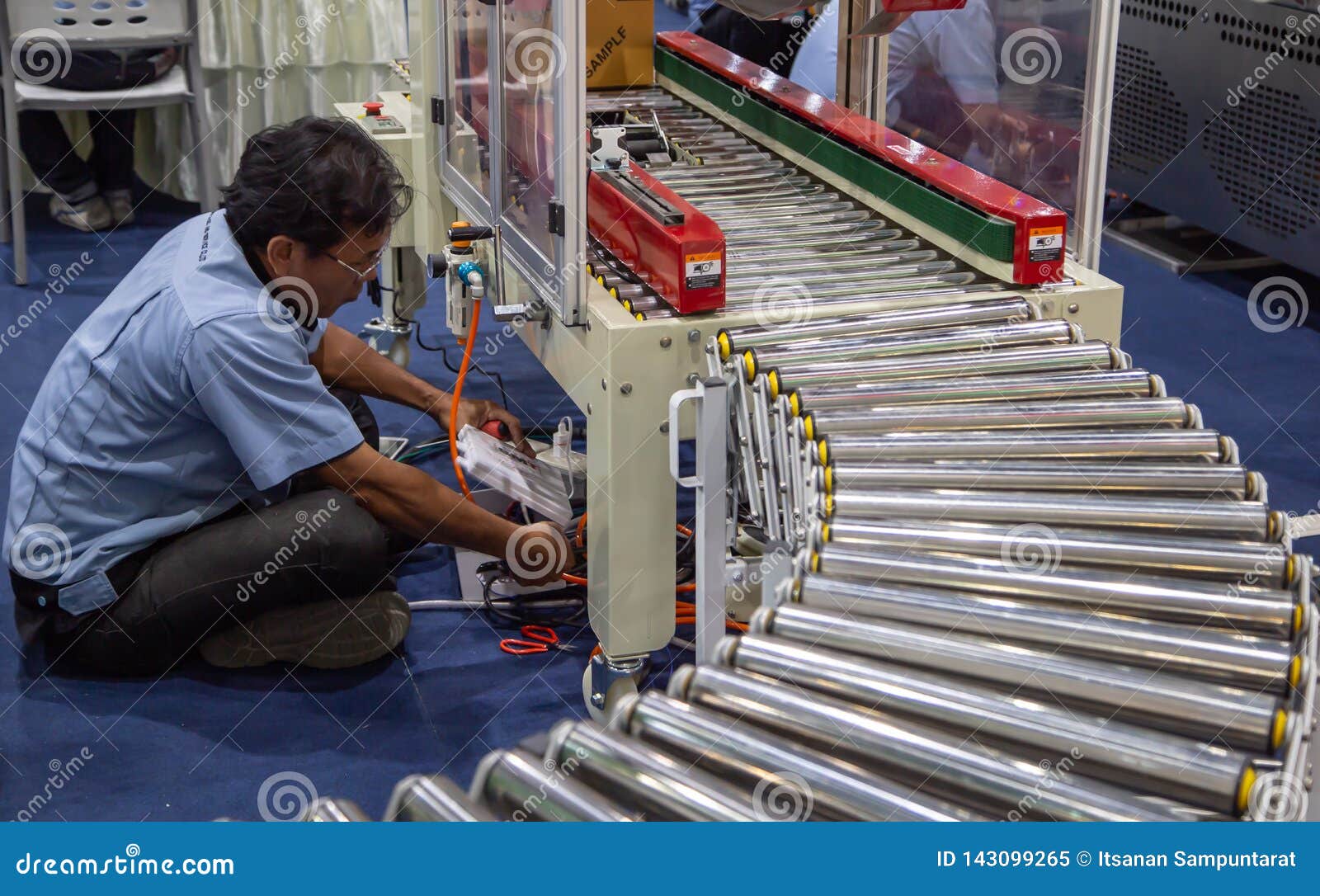
Final Thought
In verdict, a comprehensive understanding of packaging equipment elements and efficient maintenance approaches is important for ideal efficiency. Regular examinations and using OEM components can dramatically reduce published here downtime, while a well-documented upkeep background fosters aggressive treatment. Utilizing licensed professionals even more improves repair service high quality and reliability. By executing these practices, companies can ensure the long life and performance of product packaging makers, ultimately adding to improved operational efficiency and reduced prices.
Effective upkeep of packaging makers hinges on a complete understanding of their key parts, consisting of the framework, drive system, and securing systems.Effective operation of packaging machines relies greatly on routine upkeep to protect against common problems that can disrupt production.Executing preventative maintenance techniques is important for maintaining the efficiency and integrity of packaging equipments. In addition, keeping precise documents of upkeep tasks aids in tracking the equipment's efficiency over time, promoting notified decision-making concerning future maintenance demands.
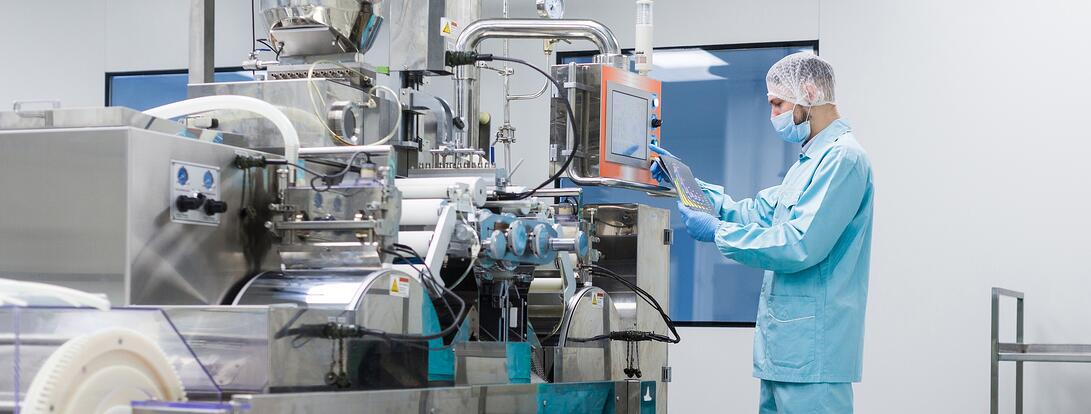
Report this page